Industrialization likes acronyms, and acronyms give it back to industrialization. MP, FA, EPM, ODM, OPM, PRD, DRP, BOM, DFX, DFM[ETC] Among these acronymic specimens, some refer to processes, others to documents… But all deal with industrialization. While each professional sector uses its own jargon, the industry sector largely supports the acronym.
The ones we will be dealing with today are in the form of EVT/DVT/PVT.
These acronyms EVT DVT PVT stand for Engineering Validation Test / Design Validation Test / Production Validation Test.
Today, we will share with you our vision of EVT/DVT/PVT, built over our years of expertise and product industrialization.
These three acronyms refer to the different stages of industrialization, between the POC and mass production: from the less mature to the most mature. These different stages exist to minimize the risk of errors during mass production. Defects in design and process are discovered during these steps; it is very important to detect them early and to detect them before going into mass production. They also help to structure the decision-making process. We start from a large number of options that we reduce to set this number of options and then only have to correct/adjust/optimize.
During EVT we validate a functional scope, during DVT we stabilize and during PVT we adapt the production. During the DVT phase on, the scope is no longer touched, but errors are corrected, elements are adjusted and performance is optimized.
We’re progressing step by step. Each step brings an additional degree of maturity and each iteration produces new prototypes. If the result of a step is not satisfactory, we iterate, keeping in mind the time/cost/quality arbitration. Each iteration has a cost and involves additional delays.
Each of these phases is cyclical and includes subphases of 1) design 2) prototype 3) validation. In general, these subphases do not exceed three step. This way you will have EVT 1 EVT 2 EVT3. The principle is the same for DVT except that the subphases will be carried out on a final product scope and using tools that will become final as the DVT progresses
Concerning the PVT, it is:
1- installation of the production line
2- review of the line
3- production test
4- FAI (first article inspection) + reports
Then identification of weak points => return to 1 for continuous improvement.
At the end of PVT, the golden and all production means are validated to go to MP (mass-production) which will also be subject to a continuous improvement movement.
Before the EVT/DVT/PVT is the prototyping phase that leads to a proof of concept. There are “looks like” prototypes that validate design, appearance, use; and “works like” proof of concept that prove product functions.
EVT : Engineering Validation Test
Définition :
Once the hardware is finalized, it needs to be tested and validated. This step is called EVT.
This EVT phase is used to verify that the prototype works with all the functionalities defined in the PRD, and that the objective of the object is well reach (example: make a vacuum cleaner that really works as a vacuum). The EVT phase therefore makes it possible to ensure that the project is not off track on the function. DFX are part of the process.
Objectives :
During pre-EVT: test everything you want to put in the product (often carry out by independent pre-studies)
During EVT: identify problems that need to be solved before design, produce prototypes offering key functionalities, with existing components or still in the development stage, in the desired size. Integrate what was in the PoC to reach at the end of EVT a fixed scope that can be achieved.
Combine looks-like and works-like prototypes into one form factor, with short series parts:
Dupli Silicone part, or part from Soft Tooling, 3D printed, Prototype PCBA
• Select the main function features & criterias (sometimes from a build matrix of options)
• Identify all of the issues that need to be fixed with that design
Quantity :
It depends on Product complexity & BOM cost (5 to 100). Between 1 and 5 items per prototyping cycle. To validate the EVT, a dozen prototypes will be required for an average product.
Means :
Rapid prototyping, 3D printing, laser cutting electronic card designed to measure; mechanics designed to measure etc.
Results :
Prototype in the required size, key features on the product. The selected components and technologies can reach the desired cost.
Deliverable :
Prototype that contains the desired functions.
Limits :
In general, prototypes are in their raw cosmetic states: no surface state, surface finish, color… But it depends on the importance of cosmetics in your product. If the design or the size are major features in your products, then your earliest prototypes and mockups must display the final design so that you can design the electronics and mechanics in relation to the final design. In general there are no optimizations (costs, technos…) and some secondary features may be missing.
DVT : Design Validation Test
is supposed to be one configuration of your final production design, made of components from production processes (and final hard tools) and on a line following production procedures.
Définition :
The DVT phase is initiated when the EVT prototype is validated and when we are certain that the design is functional. The DVT is used to perform the validations points that the customer requests on a fixed design. It’s rare that the design to be correct at the first time, so we iterate on the design until the product to be perfect.
During the DVT, we test the design with real products in the right dimensions and with materials that are close to what we want to obtain. In the same time, it’s necessary to contact the suppliers to start producing the various final parts.
In the middle/end of the phase, even the injected parts are tested. We will use the final molds that will be adjusted as we go along (minor corrections, surface treatment, parameter adjustment, debugging and denoising for electronics…). At the end of the phase we must have a product with validated final specifications because ideally the PVT phase is only used to validate the means of production (assembly line, jigs and test bench…)
During this DVT phase, it is possible to choose parts or materials voluntarily temporary, to product in few specimens (ex: injected parts but with silicone mold which will last only about twenthy injections but will allow to make validation tests). Note, in duplicate silicone, we rarely exceed 20 parts runs. Indeed, with this technology, the PU used are bi-components Isocyanate and polyol. Once these 2 components have been mixed, and once the casting has been carried out, the vacuuming carried out and the pot life time has passed, the material becomes exothermic. It therefore attacks the silicone on the surface as it measures pulls. The fact that the parts must then be unmoulded by twisting and deforming the moulds (such as silicone moulds for cakes) also damages the properties of the silicone mould. At this stage, it is better to use all the final components. Unless we decide to market the PU parts, or 3D printing for economic or marketing reasons. It’s a practice.
The product must be designed in small quantities and subjected to different stresses in order to test strength, tightness, safety… A large battery of tests will be required to determine whether the product is ready for production or not. Like the EVT, DFXs are worked on during this stage.
DVT products are used for all laboratory validations (Aging, Thermal and climatic cycle, vibration, packaging, waste, chemical resistance, biocomp…) It is also at this stage that certification issues are integrated. During the DVT phase, products should only use parts from medium production runs. And not parts via Dupli Silicone.
Objectives :
To produce prototypes with full functionalities, with components intended for mass production, that can be used for certification (CE) and identify potential problems that need to be solved before design.
Realize/industrialize and reject what is ultimately not feasible or too expensive (quality vs. functions vs. price vs. sales target) to achieve a final product at the end of the phase.
Verify mass production yields (Based on the one configuration of the final design for each shipping SKU)
Qualify the first final hard tools for every part in the assembly
Quantity :
Generally between 30 and 200 specimens, depending on the volume in MP (mass-production) and the cost of a prototype. Certification requires a certain number of specimen and validation consumes at least 20 to 30 prototypes by itself. Not to mention those necessary for marketing.
Means :
Rapid prototyping, custom components; custom mechanics, industrial equipment.
Deliverable :
validation document for all tests, frozen 3Ds and squared off.
Results :
functional prototypes, ready for mass production, without major defects. Some prototypes can be distributed to “beta testers” or shown to future customers. DVT’s can be used for certification tests.
Limits :
Mechanical parts are not final and their cosmetic appearance may be imperfect.
PVT : Production Validation Test
Is the “last build”; the units you are made are supposedly intended to be sold to customers, if they pass all of your test stations. PVT typically transitions directly into Ramp-Up and Mass Production.
Définition :
PVT is the last phase of industrialization, the final step before mass production that allows the first products to be sent to customers, often the backers of crowdfunding platforms. During this PVT phase, the design is frozen and the assembly process is validated. The parts are close to the series but assembled by hand. The assembly line assembly is simulated to test the assembly process.
It is therefore at this stage that the assembler executes the planned production line(s) using all final equipment, processes and quality assurance steps.
During the PVT phase, DFXs are corrected, test benches and mass production moulds are designed and ideally small mechanical adjustments are made. It is very common at this stage to find assembly problems, and this may include design changes to plastics and PCBAs to minimize performance waste, optimize assembly if the cost impact is significant or optimize some parts if the FMECA reveals weaknesses…. All components and processes must be at the planned mass production stage, including packaging, logistics, freight forwarding and quality assurance controls.
The production line must be optimized for the product, reducing the time between each step if possible, and making the entire process as smooth and reliable as possible.
Quantity :
between 50 and 200 items.
Objectives :
To verify mass production yields at mass production rates. Prove that the factory production and testing process is operational -> we take a finished product and we build a production line optimized for the series.
Moyens :
Electronics and final components. Mechanical parts from production moulds.
Results :
Validation that the products at the end of the product line are in conformity with the design.
Delivrable : final product in limited quantity.
Limites :
Time required for production may still be high. Not all procedures are yet written.
All these major steps have been simplified to make this article digestible. Whatever happens, making a product is a great adventure and a long journey. Having an overview of the different steps, even if it is quick, can help you avoid problems.
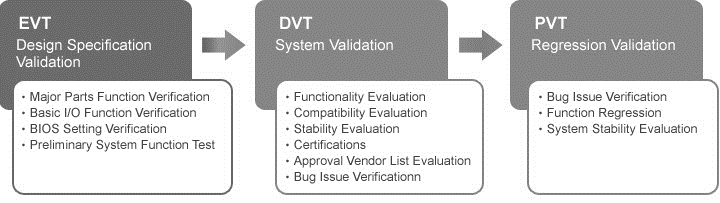
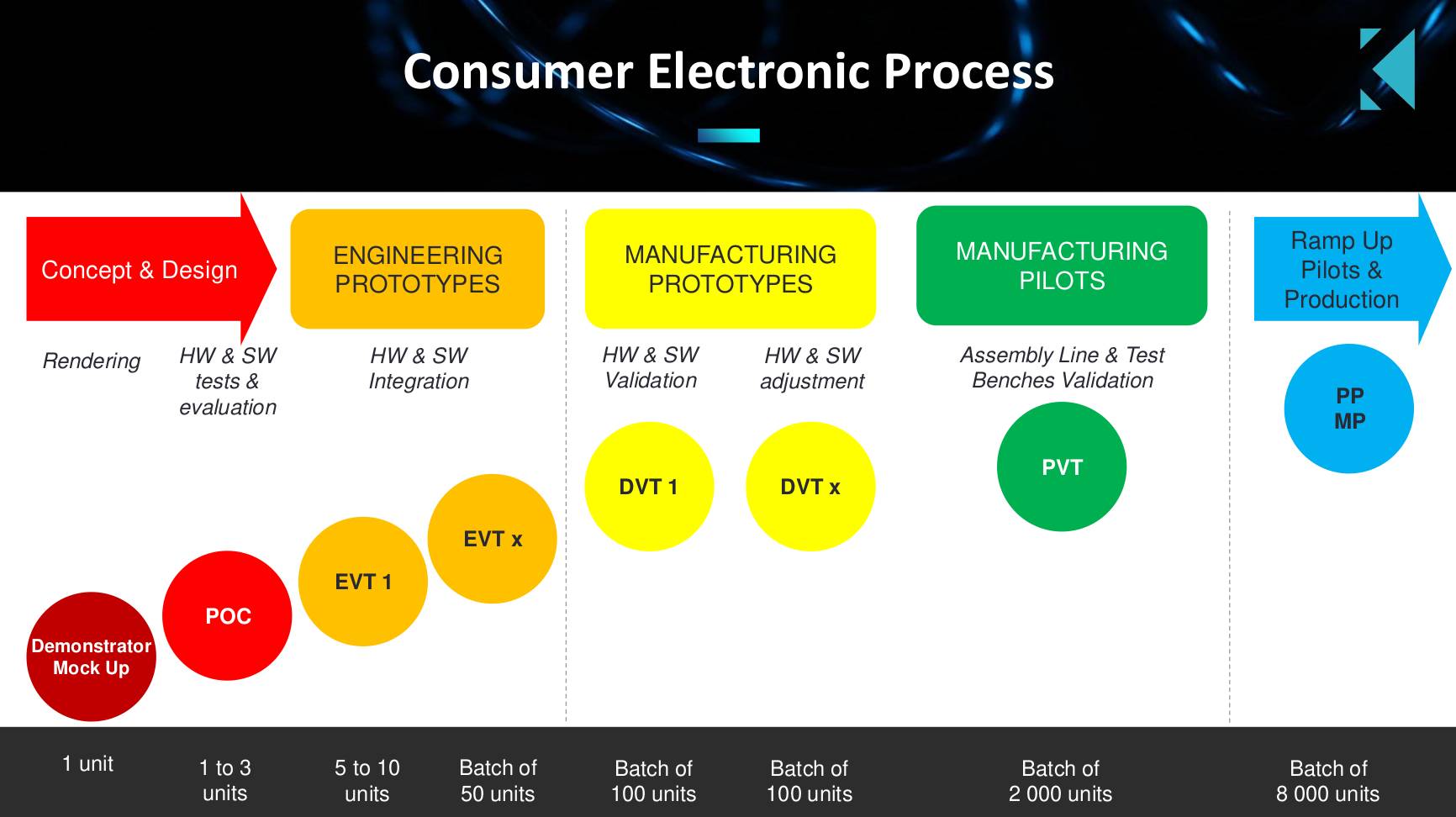
Glossary
DFX : Design for X
All the processes to optimize the design of a product
- “DFA Design for Assembly : product design optimize for assembly
- DFM Design For Manufacturing ou Design For Manufacturability : product design optimize for manufacture
- DFMA 1/ Design for Manufacturing (ou Manufacturability) and Assembly product design for manufacture and assembly 2/ Design for Maintenance : product design for maintenace
- DFP Design For Producibility : product design for productibility
- DFP Design For Procurement :components or supply chain to simplify mass production
- DFR Design for Reliability : product design for fiability
- DFS Design for Services product design for services
POC : Proof of concept. Prototype to prove the feasability of a concept. Before the product cycle development, the functional prototype.
PRD : Product requirement document. A PRD provides details about product to allow development team to understand capacities, fonctionnalites and characteristics of the product, required the reach the identified market needs.