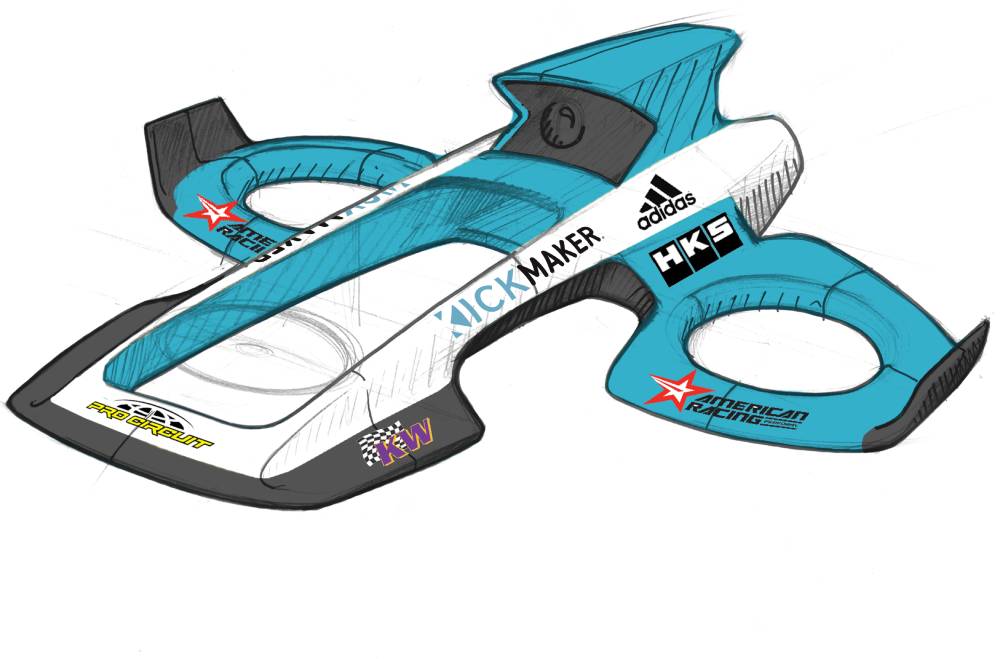
Design at Kickmaker is a technical design activity, according to the Anglo-Saxon meaning of the term (design=conception), the aim being to determine the homogeneous structure of a product in order to resolve all the industrial constraints associated with it, taking into account the technical, economic, ergonomic and functional constraints.
We do not do industrial design as such, but work in close collaboration with design agencies such as Elium or OVA. Nevertheless, on certain occasions, we can be a source of design proposals.
A tripartite product creation process
The process of creating a product is a tripartite creative process characterized by a large, multi-faceted discussion involving Kickmaker, the client and the design agency.
In most cases, the client consults first with a design agency and then with its industrial partners. We only act as a second point of contact.
The client therefore contacts the designers who define the external appearance of the product, the first functionalities and provide us with the first drawings, or 3D files representing essentially the external surfaces.
Then the exchanges begin. We take note of their proposals, study them and determine what is feasible or not according to the technical possibilities, the adequacy with the expected functionalities, the budgetary constraints, and then send our comments in turn.
Taking these comments into account, the designers make new proposals, the client selects one, we retrieve it and then start working on it to make an industrializable model. We start from technical specifications. We integrate from the beginning all the ergonomic and usage constraints of the product. We exchange with the client, looking for the most exhaustive information possible, putting him face to face with his product in concrete use cases, and we try to define everything that is not industrial and that is not purely engineering.
Then, we invite mechanical, electronic, mechatronic teams to floor on the subject. We formalize the design concepts by 3D modeling which allows us to obtain perspective representations of the designed products and to describe their uses. We think about the choice of materials according to technical constraints, the management of large assemblies, the industrialization process, the control of production costs as well as the cost price, and the future industrial partners who will be able to produce the object.
As an industrialist, we correlate the aesthetic and practical dimension and the “manufacturability” of the product. Our first role is to accompany design agencies in the maturation of their product.
Once the industrialisable model has been produced and sent to the design agency, the roles are reversed and it is they who give us feedback. We enter a phase of fine finishing touches.
This tripartite creation process is a journey marked by negotiations between aesthetics, use, ergonomics, functionality and industrial feasibility. The result is a compromise between the different stakeholders.
Friction points: a design too far removed from industrial constraints
Agencies are sometimes too far removed from the problems and industrial constraints of product creation. They imagine products that are difficult to conceive industrially. In this case, we take over the design.
Some agencies, on the contrary, carry out in-depth work, for example on structural strength, assembly, man/machine interfaces, and then facilitate exchanges between the various protagonists (them, us and the client).
They know, for example, that the realisation of such a volume involves splitting it into several parts.
Industrial design-oriented design agencies with experience and who already work with design offices have a better understanding of industrial constraints (e.g. geometric compatibility with materials). They provide more advanced preliminary work, which takes into account production issues.
Constraints can be of several types :
– space constraints: while electronics is more modular, constraints crystallize at the level of mechanical mechanisms and batteries. The technological limit sometimes constrains the dimensions of the object.
– manufacturing constraints: the product must be mouldable, demouldable. The large smooth surfaces often desired by agencies are complicated to achieve. It is then necessary to think about the location of the parting lines.
– material constraints: solidity, rendering, special characteristics (transparency), biocompatibility, eco-design…
Kickmaker’s micro-factory
Thanks to the micro-factory dedicated to the assembly of high-tech products that we have named KAL for Kickmaker Assembly Line, we prototype, iterate, test many shapes and materials. We offer ourselves the means to be quite reactive. Kickmaker engineers have a big maker component, a more open vision than a classical engineer with multiple skills. We don’t just run a specification file, but we look for innovation and optimization. In many cases, we go beyond classical engineering because we work on many innovative projects that require research into processes, materials, technologies, industrial partners. We have a pool of talents who know how to do things themselves, with a design approach. We can start to test a design with 3D printers, mechanical properties (clips, screw drums, interlocking) or aesthetic rendering in terms of materials: moving from all plastic to bio-sourced products for example, or using our extensive network of suppliers and prototypists. Thanks to KAL, we can make small-series semi-finished products or functional finished products with the materials, as well as assembly lines, assembly line setups, pre-certification tests.