Découvrez nos articles « spécial Made in France », une série de témoignages d’entrepreneurs hardware ayant tenté le Made in France. Vous y découvrirez leurs aventures uniques, leurs expériences et leurs retours terrains, qu’ils soient positifs ou négatifs mais toujours sans langue de bois.
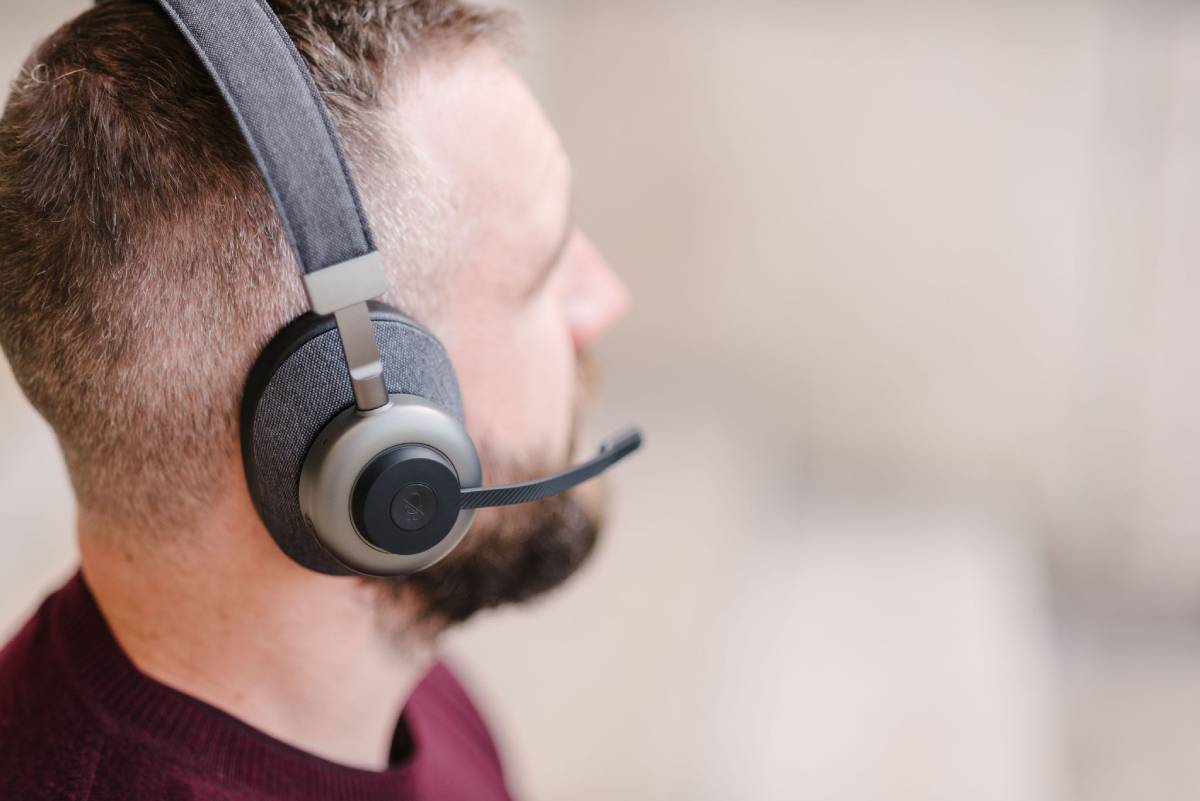
Loin de l’évangélisation actuelle autour du Made in France, questionnons-nous sur la possibilité d’un produit high-tech 100% Made in France. Vous lirez au cours de ce récit que c’est aujourd’hui impossible, et que les arbitrages de conception sino-français sont légion dans la production high-tech.
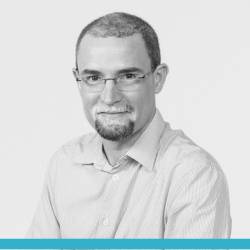
Découvrez le témoignage de Martin Pourriot
– Head Of Hardware and Manufacturing at Orosound.
Sommaire
- Le côté rassurant de la Chine pour un premier produit
- Un glissement progressif vers le Made in France : une question d’arbitrage entre conviction et rationalité.
- Un mix de production Franco-Chinois , habituel dans l’électronique.
- La maîtrise de sa technologie : un impératif pour une entreprise.
- La production, un gros morceau
Le côté rassurant de la Chine pour un premier produit.
Tilde® Air, le tout premier casque de la marque Orosound, est un produit typé grand public, complexe sur le plan de l’assemblage, car il comprend beaucoup d’opérations et une BOM mécanique assez étoffée. Cela induit beaucoup de main d’œuvre pour du made in France.
Pour un premier produit, il était par ailleurs exclu de travailler avec un industriel qui n’avait pas d’expertise dans l’audio portable. L’avantage de la Chine est qu’elle concentre un grand nombre d’industriels spécialisés dans le son et l’audio, c’est rassurant. Nous nous sommes donc tournés vers un industriel chinois afin de prouver que notre technologie était industrialisable.
Un glissement progressif vers le Made in France : une question d’arbitrage entre conviction et rationalité.
Pour le second produit, Tilde® Pro, c’était une autre histoire. Nous avions gagné en confiance et en technicité. Nous pouvions nous permettre d’envisager une production Made in France, en partie tout du moins. Pour être clair, notre produit n’est pas 100% Made in France : c’est aujourd’hui impossible dans l’électronique grand public. Lorsque vous vous rendez sur des salons consacrés au made in France, vous constatez d’ailleurs que la grande majorité des produits ont une nomenclature faiblement complexe, sans électronique.. Mais quand il s’agit d’électronique, certains composants n’existent tout simplement pas en France.
Pour autant, même si le produit n’est pas 100% français, les valeurs et convictions de l’entreprise sont fortes.
Plusieurs déterminants peuvent pousser une entreprise à faire du Made in France.
Pour nous, c’est non seulement un critère de différenciation, mais également une valeur qui nous correspond, qui nous fédère et à laquelle nous sommes attachés.
Ajoutez à cela des déterminants rationnels, liés à la difficulté pour une entreprise de faire du Made in China :
- La fatigue induite par les déplacements. 5 ou 6 déplacements en Chine par an, et parfois sur de longues périodes, c’est éprouvant pour les équipes.
- Le fait que, lorsque vous développez un produit innovant, vous consommez plus de temps ingénieur à l’industriel. Vous passez donc après des produits plus classiques, plus simples à fabriquer.
Cela soulève également des questions rationnelles et environnementales : lorsque vous faites du hardware, vous développez une plateforme électronique avec des composants que vous allez choisir et acheter vous-même. Vous contactez des fournisseurs avec qui vous négociez des prix. Dans les phases de conception, vous n’allez pas forcément chercher des fournisseurs chinois pour avoir des composants chinois. Vous vous retrouvez donc dans une situation assez étrange qui fait que vous avez négocié des prix en France sur des composants que vous allez envoyer en Chine (ex : composants STMicroelectronics) pour ensuite faire revenir les produits en France, et les renvoyer en Chine et ainsi de suite. Tout cela induit de la friction : délai, taxes douanières à l’entrée, problèmes de transporteur, de traduction…
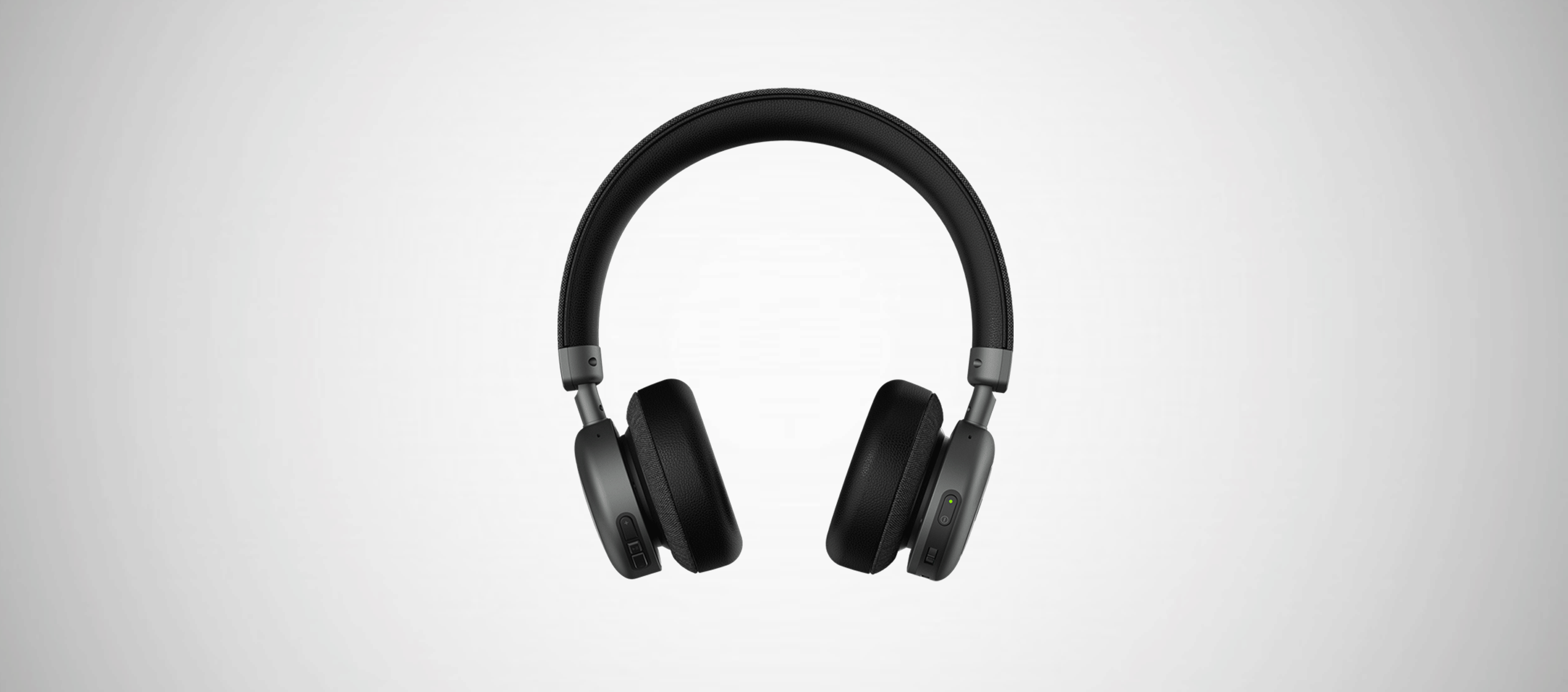
Un mix de production Franco-Chinois , habituel dans l’électronique
Mix sino-français
Pour répondre en partie à ces problématiques, nous avons décidé de réaliser la carte électronique en France, qui contient notre technologie brevetée. On effectue également une transformation, considérée comme substantielle par les autorités douanières, en France : nous procédons à une mesure acoustique produit par produit, pour ajuster unitairement les traitements électroniques sur les propriétés physiques mesurées. En deux mots, l’ensemble des tests audio spécifiques à notre technologie, ainsi que les tests de qualité sont réalisés en France.
Pour ce qui est des activités consommatrices de main d’œuvre, on les conserve pour l’instant en Chine. Les pièces mécaniques viennent de Chine et nous réalisons les opérations d’assemblage final en France.
Un mouvement de relocalisation
On aime dire qu’on est dans un mouvement de relocalisation : on ramène progressivement des briques de production en France. Une partie de notre supply chain est désormais en France. C’est un autre relationnel de travailler avec un industriel français, ce ne sont pas non plus les mêmes modèles de service de manufacturier. Le relationnel est rarement évoqué lorsqu’on parle de relocalisation, et pourtant, c’est un élément clé.
Ce que l’on trouve souvent en Chine, c’est le modèle ODM/OEM. Cela signifie qu’ils vous offrent le service complet et la tête de pont. Ils gèrent toute la supply chain amont. En gros, vous arrivez avec une spécification et le partenaire chinois fait ensuite une grosse partie du design dans le détail, et va éditer toutes les specs de tous les sous-composants. C’est une énorme facilité proposée aux porteurs de projet. Pour une petite entreprise, la gestion de production, avec tout ce que cela implique : gestion de trésorerie fournisseur, gestion des paiements etc, peut être extrêmement lourde.
Quid de la contrefaçon
Il y a aussi la question de la contrefaçon. On sait qu’elle existe, on a cette inquiétude. On essaye donc d’en discuter de manière “business” avec les industriels chinois. Ils sont en général plutôt ouverts. Sur le casque Tilde® Air, nous avons travaillé avec une usine qui souhaitait se développer sur les nouvelles technologies liées à notre domaine. Nous avons donc trouvé un terrain d’entente : on lui apportait les briques technologiques qui l’intéressait, en contrepartie, elle offrait le service industriel de design et de conception.
Pour travailler avec la Chine, il est illusoire de chercher à verrouiller l’innovation. Mieux vaut se placer sur un terrain collaboratif. Cela dit, nous avions tout de même sécurisé l’accès à notre logiciel embarqué par du cryptage. Ainsi, le design mécanique pouvait être copié, mais pas le logiciel.
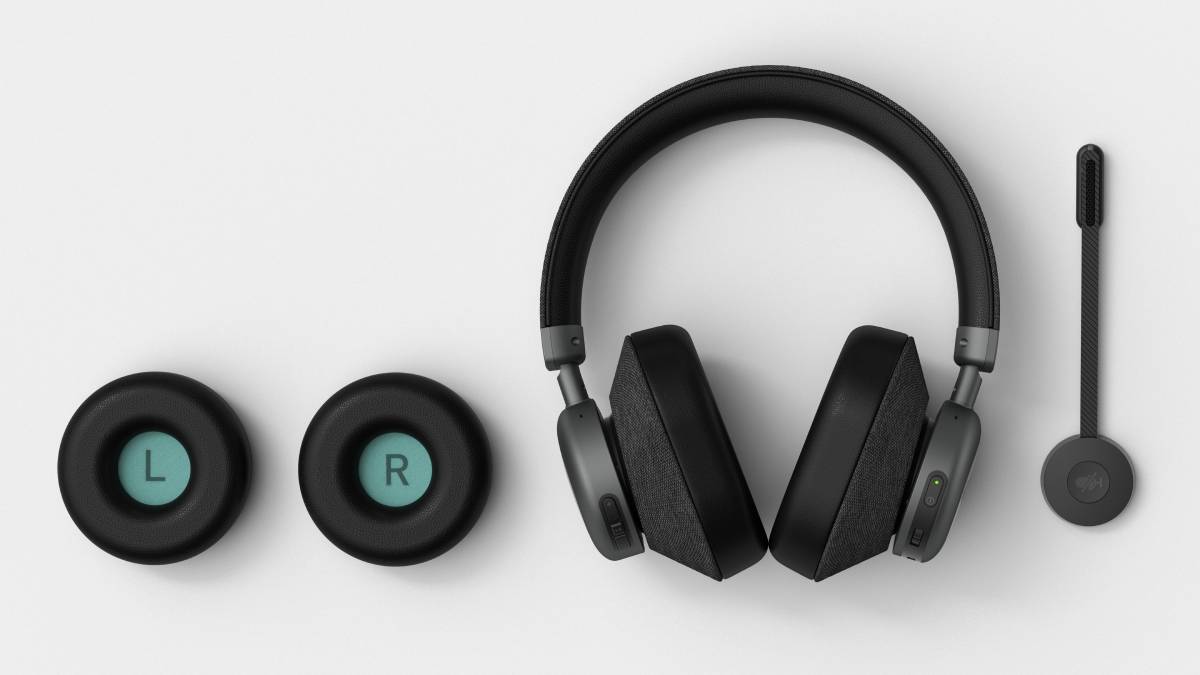
Contrôler sa technologie : un impératif pour une startup industrielle.
Avec le casque Tilde® Pro produit en France, nous avons le contrôle sur la technologie. Il est déterminant pour une entreprise hardware de contrôler son design électronique. C’est le cœur du sujet et une condition sine qua non pour innover.
Attention par contre : ce n’est pas parce que vous faîtes appel à un bureau d’étude français que vous avez forcément le contrôle sur votre design.
Contrôler sa technologie pour faire évoluer son design
Dans la vie normale des produits électroniques qui ne sont pas forcément à la frontière de l’innovation, vous cherchez à figer l’électronique une fois que vous avez fait votre développement et que le cycle en V est terminé.
Dans le cas d’Orosound, nous avions besoin de rendre ce design évolutif : vous reprenez votre design, car soudainement sort un nouveau composant, ou vous devez faire des corrections, ou vous vous rendez compte d’interférences mal maîtrisées, ou vous avez besoin d’ajouter une nouvelle fonction… Donc, non seulement, vous avez besoin d’un design éditable, mais vous avez également besoin de la ressource, de la personne qui a fait le design. C’est une ressource rare, il faut s’organiser pour y avoir accès même lorsque le produit est en production ! Et c’est d’autant plus important si vous souhaitez développer des versions ultérieures de votre produit : vous n’allez pas à chaque fois repartir de 0. À chaque design des problématiques propres : on apprend à chaque produit, mais il faut aussi savoir capitaliser.
[Chez Kickmaker, nous avons créé la KAL, notre micro-usine urbaine, pour permettre aux entrepreneurs de développer, d’itérer et d’assembler leurs produits au plus proche de leurs équipes. Ainsi, ils maîtrisent leur technologie, leur produit, leur innovation.]
« Vous reprenez votre design, car soudainement sort un nouveau composant, ou vous devez faire des corrections, ou vous vous rendez compte d’interférences mal maîtrisées, ou vous avez besoin d’ajouter une nouvelle fonction… Donc, non seulement, vous avez besoin d’un design éditable, mais vous avez également besoin de la ressource, de la personne qui a fait le design. C’est une ressource rare, il faut s’organiser pour y avoir accès même lorsque le produit est en production ! »
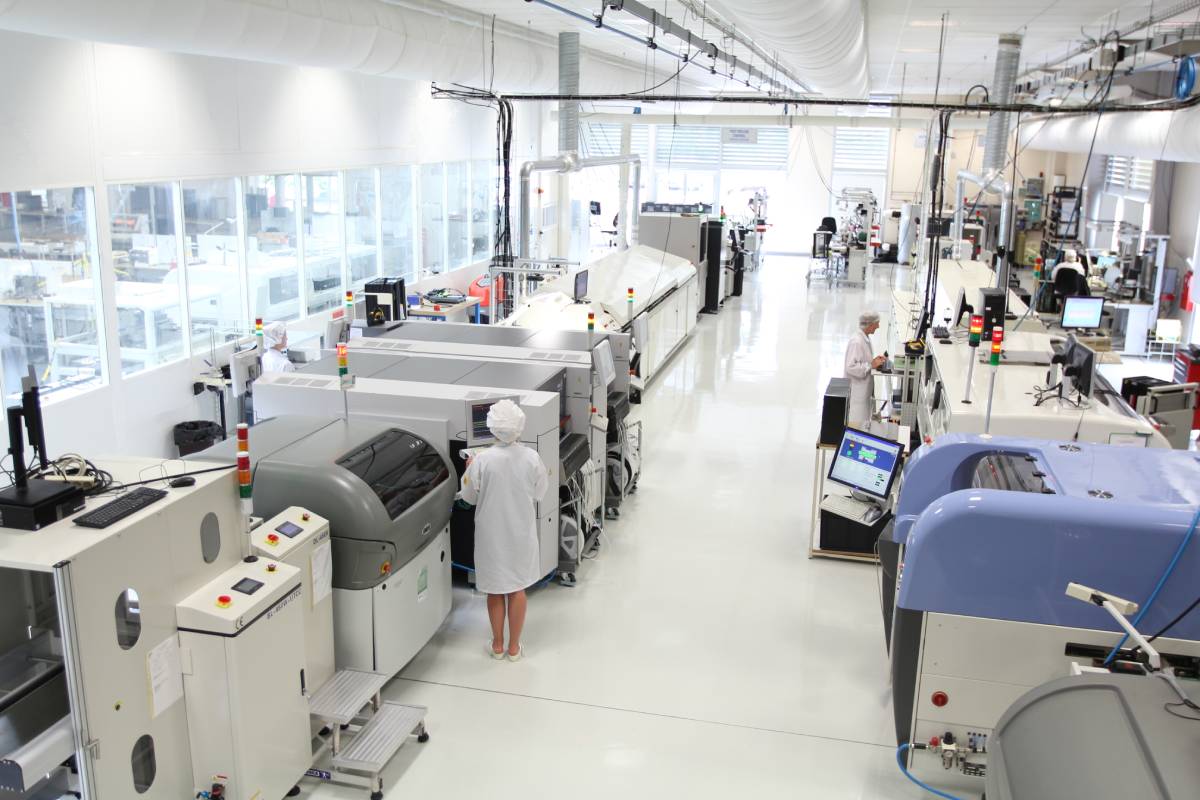
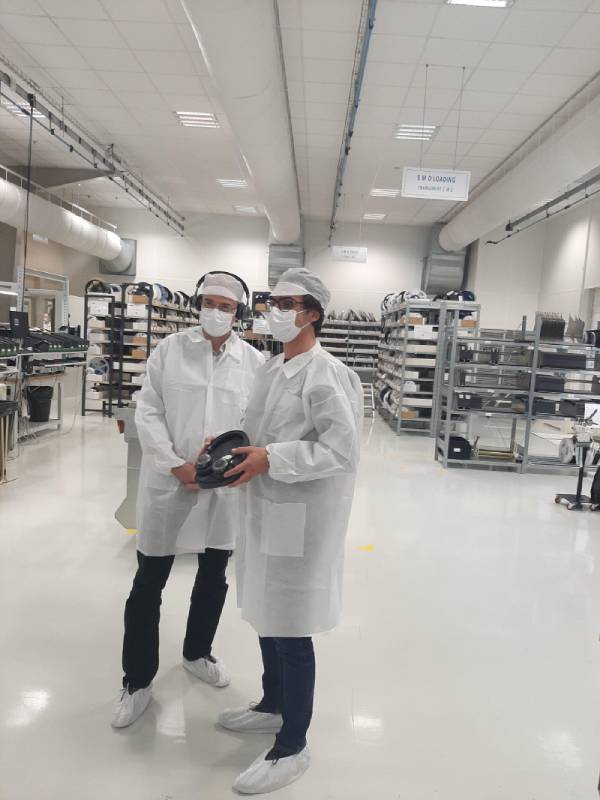
La production, un gros morceau
La première série
Nous avons réalisé la première présérie avant le COVID, la deuxième en juin 2020 et la production est en route depuis l’été. Pourtant, la partie n’était pas gagnée d’avance. Il existe une espèce de dogme dans le secteur électronique en France depuis la période d’explosion de l’IOT qui fait que, si vous arrivez chez un sous-traitant qui est un EMS français, il va dans la majorité des cas vous dire que votre projet ne l’intéresse pas.
Ils ont été beaucoup échaudés sur des types de projets IOT grand public. Or, souvent dans ce secteur, ce que les startups ont à vendre c’est elle-même, et non un produit. Les EMS ont beaucoup essuyé les plâtres sur ce genre de projet, et n’ont pas forcément eu de retour sur investissement en termes de volume de production.
De plus, le consumer electronic est compliqué, c’est extrêmement compétitif. Il faut une marque forte pour justifier les marges importantes. C’est aussi pour ça que les investisseurs rechignent à investir dans du consumer electronic. Dans notre cas, nous avons une stratégie BtoB qui s’appuie sur un réseau de distribution professionnelle, de grosses entreprises françaises qui s’équipent. C’est plus sécurisant.
Tout l’aspect DFM et industriel de la conception carte a été pris en compte dès le départ dans la phase de design, avec un concepteur de cartes interne. Il y a eu un travail pas toujours évident pour que les préséries servent à la fois à valider des aspects de conception de produit, mais aussi des aspects d’équipements de production, de logiciels de test. Le suivi et la notification des changements dans ces phases n’obéit pas à la même culture en Chine et en France.
De plus, le consumer electronic est compliqué, c’est extrêmement compétitif. Il faut une marque forte pour justifier les marges importantes. C’est aussi pour ça que les investisseurs rechignent à investir dans du consumer electronic.
Les volumes projetés.
Il y a toujours un impératif de volume pour intéresser un industriel à une affaire. Le partenaire industriel que nous avons choisi était de la bonne dimension. Néanmoins, il a parfois fallu répondre à des demandes impliquant des augmentations ponctuelles de production, pas toujours évidentes à gérer pour la partie intégration. Heureusement, Asica fait partie d’un groupe avec plusieurs sites. On a dupliqué la ligne à Granville en janvier 2021 et doublé nos capacités de production.
Arbitrage Chine France
L’arbitrage Chine-France permet donc de faire évoluer la conception du produit. Il faut qu’il y ait une interface relativement simple et détourée entre ce qui est fait en France et ce qui est fait en Chine. Par exemple, nous avons opté pour un connecteur interne sur notre carte électronique qui permet de la connecter à tous les éléments du casque. Nous n’avons donc pas de soudures à faire et cela permet de tester les signaux électriques, micro et haut-parleur sans impliquer trop d’opérations
Nous sommes actuellement en train d’étudier la possibilité de pousser notre engagement plus loin en faisant du Made in France mécanique. Les moules peuvent vite être très onéreux en France, et sont donc seulement pertinents sur des volumes importants. Je pousse actuellement la réflexion sur une fabrication type usinage numérique pour certains projets. Cela peut paraître ambitieux, mais en Chine ils savent le faire, il n’y a donc pas de raisons pour que l’on en soit incapables en France. Il y a d’ailleurs pas mal d’avantages : itérations de développement produit plus flexibles, plus de matières disponibles, recyclabilité des matières et potentiellement conception déclinable en plusieurs versions. Bref, nous sommes sans arrêt en train de nous questionner pour faire évoluer notre produit.
Bref, nous sommes sans arrêt en train de nous questionner pour faire évoluer notre produit.
En conclusion
Faire du hardware est un long parcours. Si je n’avais qu’un seul conseil à garder pour nos lecteurs : faire en sorte que les ressources qui ont conçu les éléments clés de votre produit restent disponibles, pour capitaliser et évoluer.
Faire du hardware est un long parcours. Si je n’avais qu’un seul conseil à garder pour nos lecteurs : faire en sorte que les ressources qui ont conçu les éléments clés de votre produit restent disponibles, pour capitaliser et évoluer.
Pour ne rien louper des actus industrielles.
Inscrivez-vous à notre newsletter. Pas plus d’une par mois, promis 😉
Commentaires récents